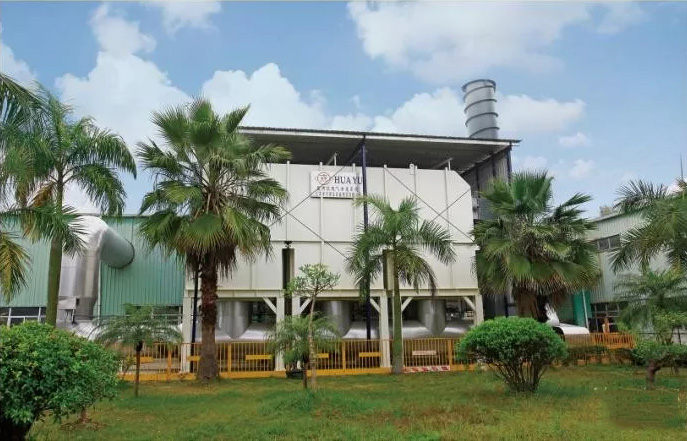
Figure 1 Arima RTO in operation
Text/Xu Haoran, Jiangsu Huayu Printing & Coating Equipment Group Co., Ltd.
Volatile Organic Compounds (Volatile Organic Compounds, VOCs) are the most common pollutants emitted by petrochemical processes and various industries that use organic solvents, such as painting, printing, pharmaceuticals, and coal chemical industries.Most of these compounds have pungent odor and toxicity, and some of them have been listed as carcinogens, such as benzene, polycyclic aromatic hydrocarbons, vinyl chloride, acetonitrile, etc., which endanger human health and pollute the air; in addition, most VOC gases are flammable and explosive, which are harmful to enterprises Threats to production safety.
Environmental protection is under pressure, and the metal packaging industry urgently needs to solve the effective treatment of VOCs
Due to the danger of VOC, many countries have promulgated laws and regulations to control the emission of VOC.The "Air Pollution Prevention and Control Law" promulgated by our country requires the purification of toxic gases produced in industrial production and the recycling of flammable gases."Comprehensive Emission Standards of Air Pollutants" (GB16297-1996) stipulates the emission standards of 33 kinds of volatile organic compounds, treats most of the other volatile organic compounds as non-methane hydrocarbons, and stipulates a unified emission standard (
As far as the metal packaging industry is concerned, since the organic solution in the coating used by most enterprises contains benzene, toluene, ethyl acetate, xylene, methyl ethyl ketone and other components, there will be Certain harmful volatiles are one of the current major players in environmental protection management.Under the high pressure of environmental protection, the metal packaging industry must solve the problem of "effective treatment of low-concentration and large-volume organic waste gas produced in color printing, coating and baking", rationally use resources, protect the environment, significantly improve the level of technical equipment in the industry, and accelerate waste gas production. The upgrading of purification devices and other related supporting equipment will break the technology and market monopoly of foreign companies in this field and improve my country's competitiveness in the world's packaging industry.
Comparison of advantages and disadvantages of three main types of VOCs treatment technology routes
The methods for removing VOCs in industrial waste gas can be divided into destructive methods and non-destructive methods.Among the destructive methods, there are three types of technical routes: direct combustion method, catalytic combustion method, and regenerative oxidation method. Among them, catalytic combustion technology and high-temperature combustion technology are currently the most common and effective VOCs treatment technologies.
The direct combustion method uses thermal combustion to oxidize and decompose malodorous gases. At an appropriate temperature, sufficient combustion oxygen and a certain residence time are provided, which can deodorize efficiently and have a high purification rate; at the same time, the main unit of the equipment works stably without clogging. It is suitable for waste gas containing catalyst deactivating substances (S, heavy metals, halogens), and viscous substances such as asphalt waste gas, etc.However, the equipment occupies a large area and the cost is relatively high.
The catalytic combustion method adopts the combination process of adsorption concentration + catalytic combustion. The whole system realizes the closed cycle of purification and desorption process. Compared with the recycling organic waste gas purification device, it does not need additional energy such as compressed air and steam, and no secondary energy is generated during the operation process. Secondary pollution, low equipment operation cost, suitable for normal temperature, large air volume, medium and low concentration, volatile organic waste gas.The one-time investment cost of equipment is relatively high.
The regenerative oxidation method adopts the alternate switching technology of preheating and heat storage, the heat exchange efficiency is as high as 90%, and the energy saving effect is remarkable.It has the functions of pre-cleaning, fire-off protection, over-temperature alarm and automatic cut-off of fuel supply.Using microcomputer automatic control and multi-point temperature control, various protection actions, operation information retrieval, and monitoring information feedback are realized, making the system safe, stable and reliable.Valve switching is more sensitive and rapid.The price of the catalyst is relatively expensive (120,000 yuan/m3), and the combustion cost of auxiliary materials is also high. It is suitable for medium and high concentrations of organic waste gas, as well as various organic waste gases generated by coating lines, printing, chemical synthesis processes (ABS synthesis), and petroleum refining processes. Exhaust places.
Generally speaking, the corresponding combustion temperature needs to be heated during the thermal catalytic combustion process. If the concentration of organic matter in the exhaust gas is high, the heat generated by the combustion of the exhaust gas can maintain the reaction temperature required for the decomposition of organic matter. Therefore, the catalytic combustion method is a kind of economically feasible method.
However, traditional catalytic combustion technology and high temperature combustion technology have low heat transfer efficiency.When the concentration of organic matter in the exhaust gas is low, a large amount of energy consumption is required, and the operating cost is high.In order to improve the thermal efficiency of the equipment and reduce the operating cost of the equipment, regenerative heating technology and regenerative catalytic combustion technology have appeared in recent years, which combine the recovery of flue gas waste heat with efficient combustion and reduce NO X (thermal nitrogen oxides) emissions. And other technologies are organically combined to achieve the dual purpose of saving energy and reducing pollutant emissions.
Evaluation criteria for selecting exhaust gas treatment equipment
Industrial waste gas treatment equipment productivity and product quality Equipment productivity and product quality mainly refer to the engineering capability of product output per unit time and equipment quality.The main features of high-efficiency equipment are: large, high-speed, automated, and electronic.
Investment cost When choosing equipment, after careful evaluation of the above-mentioned factors, the initial investment of equipment and a reasonable balance of investment should also be considered, that is, the payback period of equipment investment and the savings brought about by the adoption of new equipment.
Manufacturability refers to the ability of equipment to meet production requirements.In addition, the equipment should be easy to operate and flexible in control; equipment with large output should have a high degree of automation; equipment for toxic and harmful operations requires automatic control or remote monitoring.
Maintainability refers to the ease of preventing and eliminating failures of systems, equipment, components, etc. through repair and maintenance.Generally speaking, if the design of the equipment is reasonable, the structure is simple, the assembly of parts is reasonable, the parts are easy to disassemble and install during maintenance, the inspection is easy, the parts have good versatility, standardization and interchangeability, then the maintainability of the equipment is good. .
When choosing equipment economically, it is required that the initial investment of the equipment is low, that is, the purchase cost of the equipment is low, the productivity of the equipment is high, the natural life is long, the maintenance and management costs are low, and labor can be saved.
Safety refers to choosing equipment that is safe and reliable in production.For corrosive equipment, attention should be paid to the reliability of the protective facilities and whether the material of the equipment meets the design requirements.In addition, attention should be paid to whether the equipment structure is advanced, whether the assembly is reasonable and firm, and whether various safety devices for predicting and preventing equipment accidents are installed.
Environmental protection means that the pollution of the environment by the harmful substances produced and discharged by the equipment must meet the requirements stipulated by the state.You should choose equipment that does not discharge or emit less "three wastes", or choose equipment that has corresponding auxiliary devices for treating "three wastes".It should also be equipped with noise reduction and sound insulation devices.
The complete set refers to the supporting condition of the equipment itself and various equipment.When selecting equipment, it is necessary to avoid the phenomenon of "big horse-drawn cart" or "small horse-drawn cart" between power equipment and production equipment, as well as the phenomenon of "top-heavy" among various production equipment.
In a broad sense, reliability refers to the maintenance of the precision and accuracy of machinery and equipment, as well as the durability of machine parts, the reliability of performing functions, and whether the operation is safe, etc.
Advantages of Regenerative High Temperature Air Combustion Technology
Regenerative high-temperature air combustion technology (High Temperature Air Combustion, HTAC) is a new combustion technology that has been widely promoted and applied in developed countries since the 1990s.It can preheat the combustion-supporting air to 800~1000℃ or above, and the oxygen content in the air in the combustion zone is 2%~21%.Compared with the traditional combustion process, the biggest feature of high-temperature air combustion is fuel saving, reduction of CO2 and NOX emissions, and reduction of combustion noise.
The world attaches great importance to the development and research of high-temperature air combustion technology, and the industry regards the promotion and application of high-temperature air combustion technology as one of the main tasks of energy saving and environmental protection in the new century.In 2014, more than 50 enterprises in China adopted this technology to renovate their printing and coating iron paint drying rooms, with an average energy-saving effect of 30%, and the NOX emission index met the government's environmental requirements.
The main features of regenerative high-temperature air combustion technology are as follows.
Substantial energy saving and carbon reduction The regenerative flue gas waste heat recovery device is used to recover the physical heat of high-temperature flue gas to the greatest extent, which can generally save energy by 10% to 70%, improve the thermal efficiency of thermal equipment, and reduce greenhouse gas (CO2) emissions by up to 10% to 70%.
The temperature distribution in the furnace is uniform, which greatly reduces NOX.By organizing oxygen-poor combustion, the flame combustion area is expanded, making the temperature distribution in the furnace even; at the same time, the emission of NOX in the flue gas is reduced by more than 40%.
Reduce equipment cost.Due to the increase of the average temperature in the furnace, the heat transfer in the furnace is enhanced, the output of thermal equipment of the same size is increased by more than 20%, and the cost of the equipment is greatly reduced.
Low calorific value fuels have a wider range of applications.Fuels with low calorific value can obtain higher furnace temperature with the help of high-temperature preheated air or high-temperature preheated gas, which expands the application range of low calorific value fuels.
Regenerative High Temperature Air Burner Technical Solution
According to the customer's technical characteristics, our company determines the specific design scheme of the regenerative burner as follows: use air single preheating, the air temperature after preheating is greater than 800°C, and the exhaust gas temperature is controlled at 100°C~200°C; the burner adopts sleeve type Structure, double burner design, one burner is used for combustion, and one burner is used for smoke exhaust; double regenerator design, the regenerator is located under the burner, using honeycomb regenerator (see below for details); A rotary four-way reversing valve is adopted; the reversing time is set at 40s.
Burner The design of the regenerative burner follows the basic technical principle of high-temperature low-oxygen air combustion, that is, to efficiently recover the waste heat of the flue gas and greatly reduce the emission of pollutants, especially NOX.
For the consideration of high efficiency and energy saving, the material of the heat storage body should have the functions of high-efficiency heat storage and high-efficiency heat exchange, as well as the characteristics of no temperature stress limitation, good structural strength at high temperature, anti-oxidation, anti-corrosion, economy, and long life.The honeycomb regenerator (Figure 3) was finally selected as the filling material for the regenerator due to its many advantages, but its switching time is short (30-70s), resulting in an increase in switching frequency, which will inevitably increase the action of the reversing valve. , so this should be fully considered when making the reversing valve.
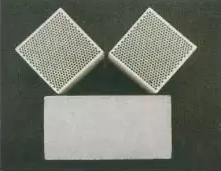
Figure 2 Honeycomb heat storage body
The reversing valve can be a rotary four-way ordinary metal reversing valve.Due to the need for frequent reversing during the operation of the burner, the life of the reversing valve will directly affect the working performance of the burner.
Advanced regenerative thermal oxidizer RTO
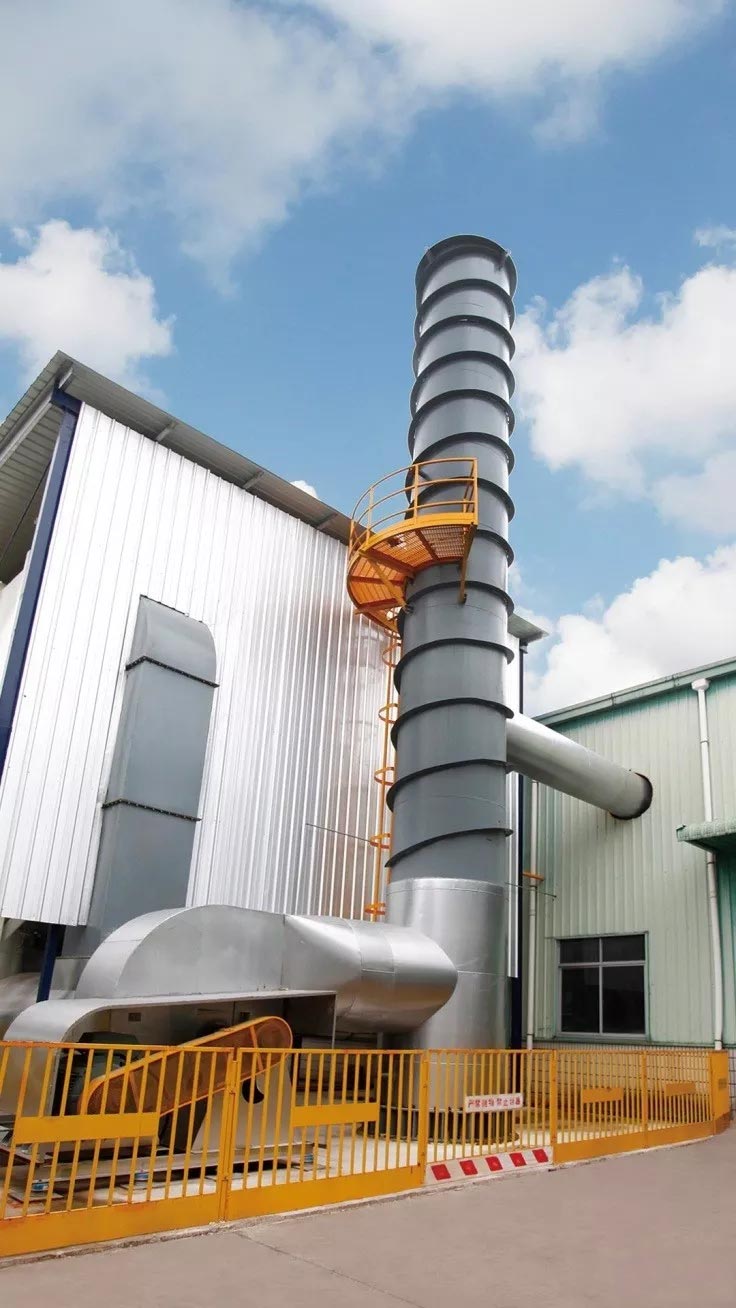
Figure 3 As an advanced version of regenerative high-temperature air burner technology, RTO is considered to be the most economical, widely applicable and durable environmental protection treatment device.
As an advanced version of the regenerative high-temperature air burner technology, the regenerative thermal oxidizer (Regenerative Thermal Oxidizer, RTO) is an energy-saving and environmentally friendly device used to treat low-to-medium concentration volatile organic waste gas. Features such as reliability, easy operation and low maintenance costs have attracted wide attention.Typical application fields include iron printing and coating industry, paint and ink manufacturing, textile and chemical electronics and other industries. It is considered to be the most economical, widely applicable and durable environmental protection treatment device.
Working principle A typical three-bed RTO main structure consists of a combustion chamber, three ceramic packing beds and six switching valves (Figure 1). ≥760°C) is decomposed and oxidized into CO2 and H2O.The regenerative ceramic packed bed heat exchanger can maximize the recovery of heat energy (heat recovery rate is greater than 95%), so that no or very little fuel can be used when dealing with VOCs.
Advantages RTO devices have the following advantages.
First, the decontamination rate (DRE) is high.The purification rate of the three-bed RTO is above 99%, and the exhaust gas fully meets the relevant national emission standards after treatment.
Second, the staged combustion technology is adopted to release heat energy under delayed combustion; the temperature in the furnace rises evenly, the burning loss is low, and the heating effect is good. There is no local high-temperature and high-oxygen zone that occurs in the traditional combustion process, which inhibits the formation of NOX, and no Secondary pollution.
Third, it is especially suitable for large air volume, low concentration of organic waste gas, and the situation where the composition of the waste gas often changes due to different products on the same production line.
Fourth, the operation cost is low, and the fuel consumption operation cost is low.When the concentration of organic waste gas is above 2000PPM, the RTO device basically does not need to add auxiliary fuel.
Fifth, up to 97% heat recovery (measured value).The temperature in the heat storage chamber increases uniformly and graded, which strengthens the heat transfer in the furnace, and the heat exchange effect is better.
Sixth, it can realize fully automatic control, simple operation, stable operation, high safety and reliability.The volume of the furnace is small, which reduces the cost of the equipment.
Seventh, the exhaust gas inlet is equipped with inert alumina ceramic balls, which can protect, buffer and filter the heat storage ceramics, so that the service life of the heat storage ceramics is longer.
Eighth, fully automatic operation reduces power consumption, and there is no waste of energy consumption due to pressure changes.
Figure 4 The purification rate of the three-bed RTO is above 99%, and the exhaust gas fully meets the relevant national emission standards after treatment.
epilogue
Among the organic waste gas treatment technologies that have been developed, applied and researched at present, the regenerative waste gas incineration treatment technology can not only effectively solve the problem that the traditional technology is not suitable for the treatment of low-concentration and large-volume organic waste gas, but also has low investment and low operating costs. , short residence time of waste gas, high efficiency, stability, complete reaction and no secondary pollution. In addition, it overcomes the shortcomings of traditional methods such as high operating costs and large reactors. It has broad application prospects in the field of VOCs pollution control.
Release time: 2022-12-05